Basic industries like energy, chemicals, petrochemicals and steel face continued challenges to improve EBITDAs which is only possible by pushing the productivity, flexibility and innovation envelope continuously. One such opportunity to transform operations and alter the cost structure is by extracting meaningful signals from the data that is generated in plants from commerce to operations. Data signatures, when analyzed holistically in conjunction with domain and process knowledge, can yield superior insights into operations. Digitization across the manufacturing lifecycle thus creates opportunities for durable competitive advantage by changing the rules of the game. Digital enablement of operations will ensure sustained and superior profitability through improved efficiency and productivity. Machine Learning and Artificial Intelligence provides unique opportunities to enable pervasive digitization.
-
Ranjan Bhattacharya
- Practice Leader, Automation & Control
Dastur with its immense knowledge of the domain and data science helps customers embrace digital enablement and transformation early and helps them establish a leadership position in the industry.
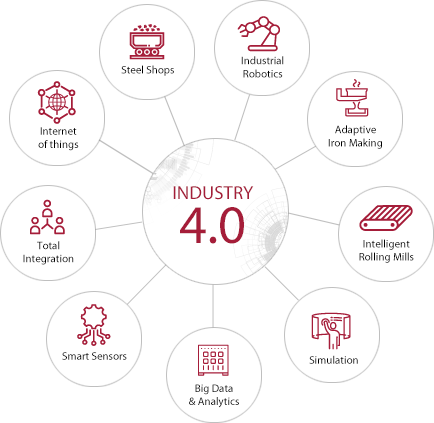
- Industrial Robotics
The focus of industries like energy, chemicals, petrochemicals is to do away with operators coming in close proximity to noxious gases, hot metals , sparks, high current systems and other human perils. Emhasis is given to smart sensors and system integration to enable robots to do things autonomously.
- Simulation
Real world problems are characterized by large-scale interdependent parameters as well as variability and uncertainties. This leads to complexity in decision making for both strategic and operational problems. DBTC’s dynamic simulation technologies and competencies, models these problems with accurate depiction of reality and corresponding solutions. They are as diverse and range from vehicle movements, scheduling, capital investment decisions, capacity analysis, plant layouts, and risk models to service center designs.
- Big data & Analytics
Big data storage will address the complex value chain, recognize patterns by monitoring the risk constantly based on the past data, analyze plant operations continuously through thermal imaging & high-speed videos, analyze the data stream for complex event processing.
- Smart Sensors
Smart sensors are the enablers for new automation function and improved performance. They help in improved tracking, data availability for the process models and data analytics. Four basic operating principles of the smart sensors are to measure, identify, communicate & track. This leads to better maintenance efficiency, condition monitoring, downtime reduction of machines.
- Total integration
Improved integration of systems & information for optimizing the total investment in terms of value chain, production, performance & services.
- Internet of things (IoT)
With IoT, digitization of production processes go beyond conventional industrial automation. The power of IoT is further enhanced with the use of the cloud where equipment from different OEMs are virtually connected and can be monitored remotely. This further benefits the user as they have to pay only for the usage of date with minimal investment in terms of infrastructure.